podpora on-line |
seriál Řezné nástroje, Technický tydeník, 2012problematika obrábění dílů pro letecký průmysl (14)
Výrazně vyšší užití titanu jako konstrukčního materiálu v civilním leteckém průmyslu začalo kolem roku 1980. Krátkou dobu po tom, co se tento materiál objevil ve vojenském letectví. Titanové slitiny efektivně konkurují slitinám hliníku i nikl-feritickým slitinám. Nové titanové slitiny nyní rapidně pronikají i do výroby dalších skupin částí letadel, jako jsou díly trupu, křídel, částí výsuvu podvozku, prvků hydraulických systémů a podobně.
Tento vývoj s sebou logicky přináší potřebu řešit inovativní způsoby technologie obrábění nových materiálů a vyřešení uspokojivé produktivity, přesnosti výrobních tolerancí a spolehlivosti procesů při výrobě takového charakteru. Firma ISCAR se tímto vývojem zabývá a přináší na trh některé typy nástrojů pro aplikace soustružení, frézování i vrtání, vyzbrojené novými jakostmi karbidů, geometrií břitů a speciálními utvářeči.
VLASTNOSTI, KTERÉ DĚLAJÍ TITAN TAK DŮLEŽITÝM PRO LETECKÝ PRŮMYSL
Volba titanu jako konstrukčního materiálu v letectví vychází z jeho některých specifických vlastností:
vysoká pevnost v poměru k měrné hmotnosti
chemická odolnost
odolnost proti korozi
výjimečné mechanické vlastnosti
malá tepelná roztažnost
CHARAKTERISTIKA A LIMITACE OBROBITELNOSTI TITANU
V leteckém průmyslu je nejpoužívanější titan 6AL-4V. Již z hlediska metalurgické charakteristiky vykazují slitiny titanu více problematický průběh obrábění a praxe plně potvrzuje, že při obrábění titanu vznikají větší řezné síly než při odpovídající aplikaci obrábění ocelí ekvivalentní tvrdosti. Navíc patří titan mezi takzvaně zpevňující materiály. To znamená, že povrchová vrstva obrobené části vykazuje větší tvrdost než původní materiál. Proto je nutné používat pozitivnější geometrii než při obrábění ocelí. Vyšší řezný odpor generuje podstatně vyšší tepelné namáhání nástroje a v důsledku nižší tepelné vodivosti titanu si i samotné třísky déle udržují teplo, čímž je nástroj namáhán ještě více. V důsledku vysokých řezných sil a tepla pak dochází ke kráterovým výmolům podél břitu a tím k rychlému opotřebení nástroje. Titan má také podstatně vyšší modul elastičnosti než ocel. V kombinaci s vyšším řezným odporem se nežádoucí vlastnost odtlačování se obrobku od nástroje ještě zvyšuje. Tenkostěnné profily mají při obrábění snahu se bortit a vibrovat. To není dobré ani pro nástroj a s rozměrovou přesností jsou rovněž problémy. Klíčem řešení situace je absolutně tuhý stroj, co možná nejpevnější upnutí obrobku a hlavně optimálně pozitivní geometrie řezného nástroje. Když tedy vše podtrhneme a sečteme, je jisté, že máme problém s produktivitou a vysokými náklady na nástroje.
TROCHOIDNÍ FRÉZOVÁNÍ - ZPŮSOB, JAK DOSÁHNOUT EFEKTIVNÍHO OBRÁBĚNÍ TITANU
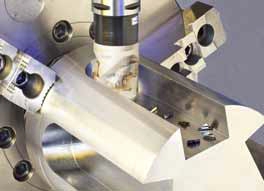
Frézování mělkých či hlubších kapes v tomto materiálu je vždy problém. Při delší době nástroje v záběru se generuje vysoká teplota. Řezné tlaky pulzují tak, jak břit vniká do řezné zóny a opouští ji, což může vést k rezonanci a vibracím. V úzké drážce je vysoká pravděpodobnost přeobrobení již oddělené třísky. Právě velký úhel opásání nástroje a poměr hloubky záběru s průměrem nástroje také vede k problémům s přehříváním nástroje a špatnému odvodu třísek. Důsledkem je pak nutnost snížení řezných parametrů a tím prudce klesá produktivita. Jedna ze strategií, jak docílit uspokojivé efektivity obrábění titanu, je trochoidní frézování. Použitím tohoto způsobu frézování drážek monolitní karbidovou frézou či čelní válcovou frézou s výměnnými břitovými destičkami lze většinu negativních vlivů eliminovat. Trochoidní nebo také spirálovité frézování spočívá v tom, že je dráha nástroje programována v kruhových drahách s přísuvem vpřed do záběru s každým cyklem. Průměr nástroje je menší než nominální šířka drážky. Pouze malá část nástroje je vždy v záběru. Tím vzniká dostatek místa pro odchod třísek ze záběru a tepelné namáhání nástroje se také snižuje. Pokud možno se doporučuje používat sousledné frézování. Pro tento způsob doporučuje ISCAR použít stopkové frézy CHATTERFREE nebo nástroje řady HELIDO, HELIMILL s výměnnými destičkami. Monolitní karbidové frézy CHATTERFREE s variabilní zubovou roztečí jsou s ohledem na svoji konstrukci výhodným nástrojem pro zhotovování drážek a kapes nejen trochoidním způsobem frézování. Nástroje vynikají vysokým stupeň odolnosti vůči vibracím a životností. Čtyř a 5břitými frézami lze na strojích s ISO40/BT40 drážkovat bez problému do hloubky 2xD do plna. Jakost karbidu IC900 s povlakem PVD TiAlN zaručuje dokonalou kombinaci mechanických vlastností pro tento způsob frézování. Alternativní způsob aplikace lze provádět čelními válcovými frézami s vyměnitelnými destičkami. Zde navíc oceníme výhodu nižšího přenosu tepla do nástroje díky řezné hraně rozdělené do segmentu z jednotlivých destiček. Navzdory svému potenciálu je trochoidní frézování výzvou nejen pro programátory, ale i pro CNC systém stroje. V každém případě musí být stroj v dobré kondici a nástroj musí být také výkonný. Oboje určuje, jak produktivní aplikace bude.
DALŠÍ PROVOZNÍ BENEFIT
Při trochoidním frézování se používá vždy menší nástroj, než je předepsaná šířka drážky. Takže jedním nástrojem lze vyrábět různé šířky drážek. Vzhledem k menším radiálním silám při tomto způsobu obrábění lze použít frézy s větším počtem zubů a tak si také dovolit vyšší minutový posuv.
PROGRAMOVÁNÍ
Donedávna měly některé konvenční programovací softwary problém s trochoidním frézováním. V takových případech musel programátor manuálně programovat kompletní cestu nástroje. Program se nedá vizuál ně zkontrolovat jinak než při běhu na stroji. Proto se donedávna tento způsob používal málo. Vývojáři CAM softwaru nedávno přidali trochoidní frézování jako jednu ze sekcí CNC programování za účelem zkrácení a zjednodušení tohoto procesu. Tím je možné celý program i graficky předem simulovat a vysledovat.
DALŠÍ APLIKACE
Především v oblasti výroby hliníkových dílů pro letecký a automobilový průmysl je často vyžadováno obrábění metodou FMR (Fast Metal Removal – rychlý odběr materiálu). Právě zde se metoda HSM jeví jako nezbytná. Při obrábění konstrukčních dílů křídel, trupů letadel a dalších obdobných tenkostěnných a rozměrných dílů z hliníku se pohybují otáčky vřetena mezi 15 000– –50 000 za minutu. Dalším polem působnosti metody HSM je oblast výroby forem a zápustek se svými požadavky vysoké přesnosti, dokonalé geometrie a kvality povrchu tvrdých nebo houževnatých materiálů. Většina aplikací vyžaduje nejen vysoké rychlosti, ale především stabilitu procesu obrábění. To vyžaduje správnou volbu nástroje a správný způsob programování, který bere v úvahu podmínky odlišné od konvenčního obrábění. Je třeba dokonale znát vlastnosti stroje a tomu také přizpůsobit řezné podmínky. Co se týká vlastností obráběcího stroje vhodného pro aplikace HSM, je nutné, aby jednotlivé díly stroje byly navrženy a sestaveny v jeden mechanicky dokonale vyvážený celek. K tomu všemu je třeba brát v úvahu vlastnosti dalších elementů celého systému, kterými jsou:
ŘEZNÉ NÁSTROJE
Kvalita a parametry řezného materiálu hrají významnou roli v procesu obrábění. Firma ISCAR vyvinula nepovlakovaný jemnozrnný karbid IC08, který je vhodný právě pro HSM metody obrábění neželezných materiálů. Jako druhou variantu pro HSM nabízí ISCAR submikronový povlakovaný karbid IC903, s 12% obsahem kobaltu a PVD povlakem TiAlN. Vyznačuje se vysokou odolností proti otěru a vysokou houževnatostí substrátu, tj. vlastnostmi, které jsou důležité při vysokorychlostním obrábění kalených ocelí (do tvrdosti 62 HRC), titanu, nerez ocelí a slitin na bázi niklu. Výměnné destičky z těchto jakostí karbidů mají specifický design a geometrii řezné hrany. Nástroje jsou konstruovány tak, aby dosáhly vysoké tuhosti, zajistily odvod tepla z místa řezu a odolávaly teplotním šokům.
UPÍNACÍ NÁŘADÍ - PROBLÉM NEVYVÁŽENOSTI
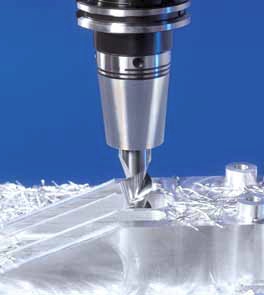 |
Příklad upnutí nástroje do integrální tepelné SHRINKIN kleštiny
|
Částmi, které podstatně rozhodují o výkonnosti HSM, jsou: vřeteno, vodicí plochy, motor pohonu, upínací nářadí a řezné nástroje. Vřeteno je patrně nejkritičtější část soustavy, a proto je třeba věnovat maximum pozornosti jeho dokonalému stavu a udržovat jeho házivost na minimu. I malá házivost vřetena nebo nástroje má totiž velký vliv na životnost monolitních fréz či destiček. Házivost břitů frézy by neměla přesahovat 10 mikronů. Životnost nástroje totiž s každými dalšími 10 mikrony házivosti klesá až o 50 %. I tehdy, když je nástroj, upínač i vřeteno přesně vyváženo, existuje stále několik dalších možných zdrojů nestability. Jedním z častých problémů bývá nepřesnost mezi upínačem a dutinou vřetena. Většinou bývá zapříčiněna nečistotami na kuželu nástroje nebo uvnitř dutiny vřetena. Při aplikaci HSM má jakákoliv nevyváženost či vibrace vliv také na přesnost výroby. Při vlastním procesu vyvažování je nutné např. pro stopkovou frézu pracující při 20 000 otáčkách za minutu vyvážit nástroj včetně upínače na hodnotu menší než 20 g x mm. Pro zajištění maximální přesnosti a tuhosti upnutí osových rotačních nástrojů vyvinula firma ISCAR systém SHRINKIN – jedná se o tepelnou jednotku a sady integrálních ER kleštin a držáků. Systém využívá efektu tepelné roztažnosti dutiny integrálních ER kleštin a lze jej používat pro upnutí stopkových karbidových fréz. Upnutí se vyznačuje dokonalou pevností, přesností a díky vlastní symetričnosti použitého upínače i uspokojivým vyvážením. SHRINKIN upínače mají protáhlý štíhlý tvar různých délek a jsou vhodné pro polodokončovací a dokončovací operace v hlubokých dutinách forem a zápustek. Pro snadnou a rychlou práci v nástrojárnách a seřizovnách nabízí ISCAR dva kompletní systémy pro SHRINKIN ER kleštiny.
Ten menší, přenosný s odporovým ohřevem lze používat i přímo u stroje. Větší mobilní jednotka s indukčním ohřevem se uplatní hlavně v nástrojárnách. Oba přístroje jsou vybaveny dokonalou teplotní regulací a kontrolou pro snadné upínání a demontáž nástrojů. Vibrace nástroje vznikají často odstředivou silou samotného osově nesymetrického nástroje roztočeného při aplikaci HSM na vyšší otáčky. Tyto vibrace se pak přenášejí na obrobek a vřeteno. Výsledkem je špatná kvalita povrchu, snížení životnosti nástroje a v neposlední řadě i nepříjemný hluk.
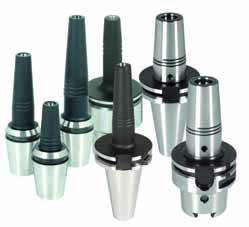 |
Typy integrálních ER-SHRINKIN kleštin
|
Pro přesné upnutí a vyvážení takových nástrojů je určen systém ISCAR BALANCIN. Jedná se o upínače opatřené sadou vyvažovacích kroužků, které mají uvnitř karbidová závaží. Po obvodu vyvažovacích kroužků je stupnice pro odečet vzájemného posunu. Proces vyvážení se provádí na běžně dostupných vyvažovacích strojích vzájemným natáčením těchto kroužků. Lze takto kompenzovat nevývažek do velikosti 61 g x mm.
ZÁVĚR
Konkurence na trhu s obráběnými díly vyvolává potřebu rychlého vývoje nových technologií obrábění a řešení problémů produktivity. Vysokorychlostní obrábění je konkrétní příklad jak zvyšovat produktivitu a snižovat náklady na výrobu. I přes vyšší spotřebu nástrojů přináší vysokorychlostní obrábění dostatek výhod ve formě zkrácení výrobních časů a případného vyloučení některých následných operací (např. ručního dokončování při výrobě forem). Ačkoli obrábění metodou HSM je známé již řadu let, jeho vývoj se dal opět do pohybu díky v poslední době narůstajícím požadavkům právě na snižování nákladů a zkracování výrobních časů.
Ing. Petr Borovan, převzato z Technického týdeníku
podrubriky seriál Řezné nástroje, Technický tydeník, 2012: